By Jack Dryden
New Wimbledon Theatre is well known as a receiving house with a long history of hosting different touring shows on our stage every week. However, what you may not know, is just how much work goes on behind the scenes to set the stage for these constantly changing productions. To find out what our technical team get up to Jack Dryden (Marketing & Sales Assistant, New Wimbledon Theatre) grabbed a hardhat and a pair of steel capped boots to work backstage with them on perhaps their biggest get-in of the year, for Matthew Bourne’s Cinderella.
Day One
Our work began at 5pm on Sunday with two lorries parked outside the theatre on Russell Road. Two lorries which, we discovered swinging the doors open, were stacked to the brim with big flight cases, steel framed pieces of set and large racks of lights. It certainly wasn’t going to be an easy afternoon! Following a short safety briefing to quickly cover what to wear, who to take instructions from and what not to do, our 30 strong team of full timers, casual staff and touring techies set to work.
The unloading process can only be described as ordered chaos. Bodies in the truck working together to tip and lower fly cases from the top of stacks onto their wheels, sending them to others to run them down the ramp where they would then be rolled onto the stage. Stand in one spot and you would quickly be in the way – as I discovered trying to take a photo of the action!

I did my best to get stuck in, guiding cases down the ramps or carrying the smaller, less intimidating items. Every box was labelled and had a place to go, ‘Rigging gear for upstage left’ or ‘ETC Ion for downstage’, the little knowledge I had from my student theatre days at least allowing me to locate the correct position on stage. Within what seemed like a matter of minutes the trucks were empty and the stage a sea of boxes, crates and bulky racks.
But our work wasn’t finished. The challenge for the rest of the evening was to clear the stage again, putting all that we had unloaded up into the rig. Lights and speakers had to be positioned on bars hanging above the stage, cables run to wire up the equipment and curtains hung to hide the lights and backstage during the show. The stage was a whir of activity and you had to keep your wits about you, minding your head for fly bars coming in and going out and your feet for boxes being trundled.
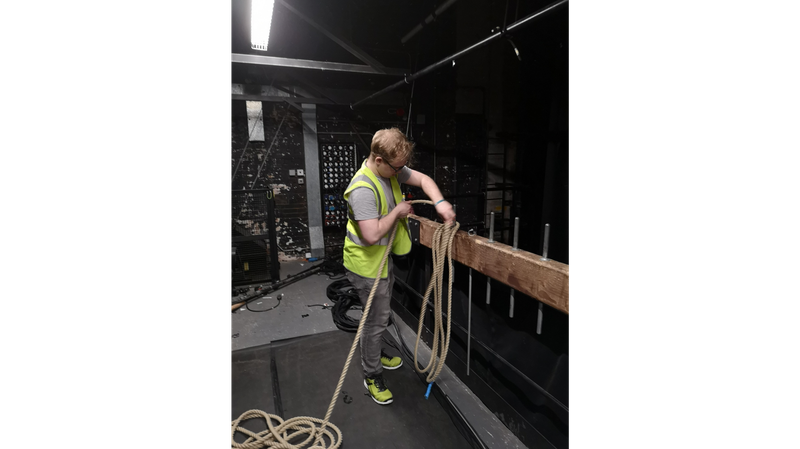
Trying to keep up with the professionals, I quickly discovered that putting things into rig is not as simple as just hanging stuff on a bar. There is a lot of knowledge and skill required before you can truly function as an effective stage hand, knowledge I really lacked. Knots were an ongoing battle. I can tie a shoelace as well as anyone, but when asked to tie a clove-hitch or a bowline, or any other knot by any other name, I didn’t have a clue. Indeed, patient as the team were in demonstrating each tie, this wasn’t much help either, as my attempts remained very much trial and error! However, I did eventually find my calling, coiling ropes no longer needed by the team to keep them away from underfoot. A small but, I’d like to imagine, vital contribution.
By the time we finished work at 9pm the majority of the rig was complete, with bars of lights and drapes hung and all surround sound speakers proficiently equipped inside the auditorium. We were left once more with an empty stage. After all that effort, it was odd to still see an empty stage. But although our work may have been largely hidden from sight, we knew how much we had done.
Day Two
When we returned at 9am on Monday morning to the familiar sight of two lorries parked outside, it would have been easy to assume they had just been left from the day before. Sadly these were different, this time carrying the main body of the set and the flooring for the show. Yes, you read that right, most shows bring their own floor to perform on!
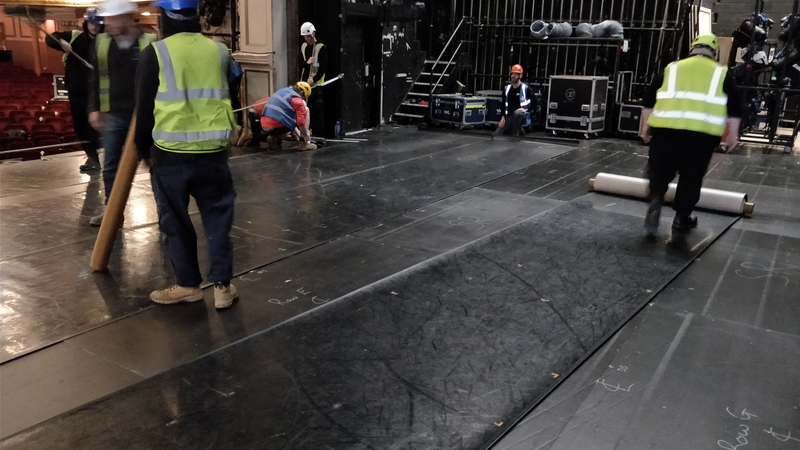
In the case of Matthew Bourne’s their floor actually consists of several layers. First, large sprung wooden boards had to be individually unloaded from the truck and tiled together on stage. These provide the bounce that allows the dancers to safely perform their routines, reducing the force that goes through their limbs as they land jumps and pirouettes. The boards are then covered by thick rubber dance mats which must be rolled out, carefully aligned, swept to remove any wrinkles or air bubbles and then taped down to prevent movement. The process took time, but it was really satisfying to see all the pieces fit together and watch the immaculate dance floor take shape beneath us.
Only after the floor was laid could we begin to unload and build the six tall towers which form the main body of the show’s set. Each standing over six metres tall, these towers had to be constructed from bulky wooden flats which were reinforced with steel and took four bodies to lift (and even then they were really heavy). Despite the weight we didn’t dare drag the flats for fear of damaging the delicate fiberglass brick texture in which they were covered to make them look like buildings.

The flats had to first be built lying down with their front face on the stage. With so much going into each building, the different teams for stage, lighting and sound had to work around each other as the flats were built. The stage team built the structure, meanwhile lighting and sound rigged and wired lights and speakers to bars within the structure. With so many bodies working together at once the towers became swarms of activity and were each built really quickly.
But then came the real fun! Each tower, now even heavier with the added frames of lights and speakers, had to be lifted and raised upright. To do so required the help of everyone on stage. Two bodies up on the fly deck hauled at ropes attached to the top of the towers, taking the edge off the weight. At the foot of the tower four bodies held the structure to keep it in place and prevent it sliding as it was lifted. Then the rest of us gathered round the front of the tower, lifting it off the ground we slowly walked forward under the front face of the tower pushing it upright.

With the six towers all built and standing, the stage team could finish for the day. However, the lighting and sound teams still had a lot of work to do testing all their equipment to make sure it was set up correctly. I helped with the lighting team as they worked on into the evening, individually checking every light in the rig. They had to make sure that all the lamps were working, and that the fixtures were focussed on the right area of the stage. It is impossible to focus the lights properly on the ground so we had to use a moving ladder and check them in position at height, moving the ladder after every couple of lights - a very time consuming process! While we worked on the rig the sound team needed to test the surround sound system, playing music and moving round the auditorium to ensure all the speakers were balanced and that the music reached every seat in the theatre. In the lighting team we finished our work around 8pm, leaving behind us the projectionist and sound engineers who worked on into the night.
Day Three
On Tuesday, with opening night that evening, there was one more lorry to unload full of props and smaller set pieces, bring our total to five trucks in all! Amongst the contents of the trailer was the staircase and London skyline, both in pieces which had to be built together. Thankfully, with only the smaller items left, nothing on this final lorry was particularly heavy or cumbersome. Nevertheless it was a great feeling to know once we were finished then all the unloading would be behind us!
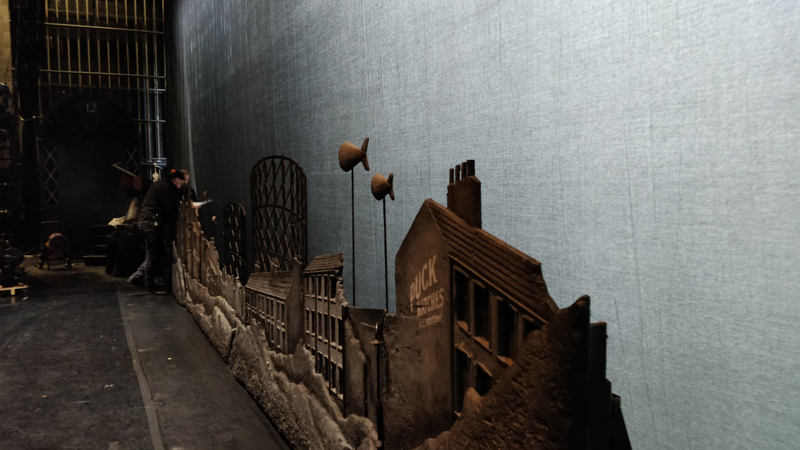
The truck contained lots of props, like the sofa, the tables, chairs and piano which were all to be used in the cafe scene. These all needed to be unloaded carefully and moved to the correct position backstage so they could be accessed quickly during the show. By the time we finished there was barely any room left in the wings, with so many props and set pieces involved in the show.

All this complete, there was just enough time to quickly sweep and mop of the stage and prepare the dressing rooms ready for the cast to arrive. The organisation for the dressing rooms was impressive, with so many wardrobes and cases to ensure that every item of costume had a place to be stored and could be easily found when it was needed.

After three days of lifting, shifting and tidying it was a relief to sit down and watch the cast do their technical rehearsal that afternoon. Joining our follow-spot operators in the upper circle, I saw how they work from a cue sheet, taking instructions from the deputy stage manager over their headsets. Theirs wasn’t an easy task, particularly given the actors weren’t in costume for the rehearsal. For each pickup they had to adjust the colour and the size of the spot, and make sure they caught the right actor at exactly the right moment. Really hard to do when they may not have seen the show before!
It was great to see how the show came together. Knowing all the work that had gone into building the set and positioning the lights, you appreciate the final effect even more. The walls collapsing as the Cafe de Paris was bombed. Lights we had placed behind the windows glowing in orange to mimic the flames left in the wake of the bombs. From five lorries full of boxes to this finished product in just three days. It was pretty amazing to see what the team had achieved.
It had been exhausting, but at least for me I knew I would be back to my desk and normality the next day. I had time for my muscles to recover and my blisters to heal. However, for our technical team this is their normal. Week in and week out they work tirelessly to put together the sets, the lights and all the tech behind the shows on our stage. Just as our audience leave the building on a Saturday night, their work begins, staying late into the night to clear the stage and get ready for the next big production. Our very own superheroes, rarely seen but without whom New Wimbledon Theatre simply could not function.
This post was originally published by New Wimbledon Theatre. If you liked it, why not follow them on Twitter or like them on Facebook for more behind the scenes blogs and videos from their team?